Кредо — постоянное развитие
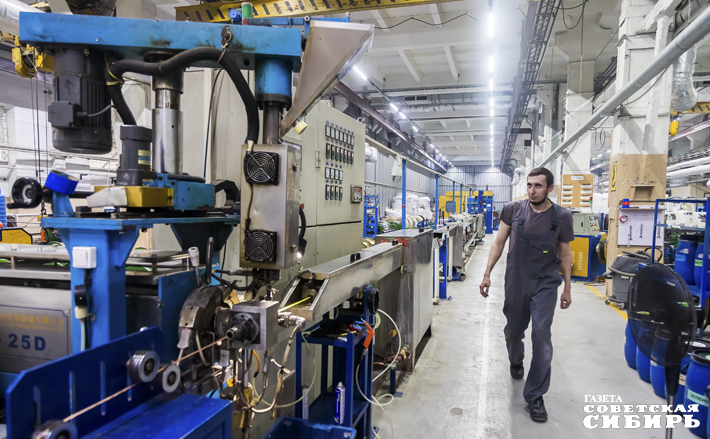
Когда компании могут больше, чем говорят прогнозы
Очередное предприятие прошло активную фазу участия в национальном проекте «Производительность труда». За шесть месяцев удалось на порядок повысить эффективность завода, где выпускают кабели, провода и шнуры для различных электроприборов.
В среднем национальный проект позволяет увеличить выработку на 50–60 процентов. Время протекания производственных процессов и объем незавершенного производства, наоборот, сокращаются примерно на 30 процентов. Это хорошие показатели, но, как отмечают эксперты, не самые главные. Дело в том, что у коллектива появляется культура постоянного развития, команда начинает работать совершенно по другим принципам.
Об этом напомнил министр экономического развития Новосибирской области Лев Решетников во время визита в компанию «ПРОМЭКО». Вместе с первым заместителем генерального директора Корпорации развития Новосибирской области Вячеславом Радионовым он оценил промежуточные результаты внедрения бережливых технологий в цехе. Напомним, реализовать проект трудовому коллективу помогают сотрудники регионального центра компетенций, который входит в состав корпорации.
В национальный проект сегодня уже вступило 142 предприятия, действующих в области. До конца 2024 года участниками могут стать еще пять.
Фото: Андрей Заржецкий
— В дальнейшем регион продолжит реализацию федеральной инициативы. В соответствии с распоряжением губернатора он будет действовать в более масштабном формате. Мы будем расширять отрасли и снижать финансовый порог для вхождения компаний, укреплять наш центр компетенций, чтобы охватить большее количество предприятий, — сообщил министр.
Если требуется особый подход
Почти 25 лет компания «ПРОМЭКО» поставляет цветной металлопрокат, электротехническую и кабельно-проводниковую продукцию предприятиям, которые функционируют в России, в том числе в Сибири и на Дальнем Востоке, на территории Союза Независимых Государств. В 2017 году было запущено собственное производство силового кабеля. В Новосибирске продукция компании использовалась при строительстве госпиталей в период эпидемии коронавирусной инфекции, нового терминала аэропорта Толмачёво, спортивного комплекса «Сибирь-Арена».
Для начала компания апробировала технологии национального проекта «Производительность труда» на семи линиях, задействованных в производстве соединительного провода. Теперь их предстоит тиражировать на остальных потоках и продуктах, и соответствующий план на ближайшие два квартала 2024 года уже разработан.
Фото: Андрей Заржецкий
— Нас обучили инструментам бережливого производства, как менять методики анализа производства и подходы к трансформации всех процессов. Конечно, были потрачены некоторые средства на улучшение, но это несущественно по сравнению с тем результатом, который мы получили, оптимизировав наши производственные процессы, — подчеркнула заместитель генерального директора компании Валентина Черняк. — Завершена активная фаза реализации национального проекта «Производительность труда». На пилотном потоке нам показали, как нужно работать с бережливыми технологиями. В полной мере реализовать полученные знания планируем на собственной производственной площадке, которую недавно приобрели. В рамках пробного проекта мы должны показывать прирост производительности труда каждый год не менее пяти процентов. На самом деле, принимая во внимание полученные опыт и результат, мы понимаем, что можем гораздо больше.
Качество без глобальных вложений
Основными проблемами, выявленными при содействии экспертов регионального центра компетенций, на эталонном участке оказались захламленность и вынужденные простои. Проходы в цехе были загромождены пустыми катушками, на которые наматывается кабель, палетами и готовой продукцией. Это могло повлиять не безопасность сотрудников, затрудняло их передвижение. На одной из линий оборудование ломалось примерно трижды в месяц. Слишком долго выполнялась перенастройка техники на выпуск другого вида продукции.
Использование философии бережливого производства позволило на десять процентов сократить время протекания процессов и объемы незавершенного производства. На 11 процентов, или на 38 минут, уменьшилось время переналадки одного станка.
Фото: Андрей Заржецкий
— Без каких-либо глобальных вложений мы повысили качество работы. Раньше много потерь было из-за поиска каких-то инструментов, сейчас все упорядочено, лежит на своих местах, подписано. Приспособления, тележки, кран-балки стоят на парковочных зонах, то есть сотрудникам не нужно ходить их искать, отвлекаться на посторонние моменты, — рассказал заместитель начальника производства компании «ПРОМЭКО» Максим Дик. — Конечно, в команде и раньше кто-то что-то знал, были попытки повысить эффективность производства, но почему-то мы не могли это сохранить, удержать, либо оно потихоньку как-то терялось. Мы прошли очень много электронных курсов, было немало тренингов. Ознакомились с хорошими практиками, когда выезжали на площадки других предприятий, где эти данные уже внедрены. Благодаря дополнительным знаниям, которые нам предоставили сотрудники регионального центра компетенций, мы поняли, что нам действительно нужно, остается контролировать эти моменты.
Стань аккредитованным специалистом
Особенно тщательно пришлось провести разъяснительную работу с коллективом. Люди не всегда сразу могут принять изменения в привычном укладе вещей. Для работников постоянно проводились лекции и обучение.
Как рассказал мастер смены Закир Фатихов, персонал проходил курсы непосредственно по бережливому производству и складированию. В результате появились места для хранения определенной продукции и тележек-рохлей. Линии оборудованы стендами с инструментами, где место для каждого дополнительно обведено, и, если, допустим, ключа нет, это сразу бросается в глаза. Таким образом удается избегать затрат на поиски.
— В первую очередь мы показывали и рассказывали, для чего это нужно, как это сделает условия труда лучше, и максимально вовлекали в процессы оптимизации. Когда мы составляли стенд для инструментов, сотрудники говорили, что и где должно храниться, — прокомментировал ситуацию Максим Дик. — То есть коллектив выдвигает свои идеи обязательно. Мы создали локальное положение о рационализаторских предложениях, информация размещена на видном месте, возле столовой. На сегодняшний день поступило 12 значимых инициатив, из которых пять уже внедрены и за которые четыре человека получили денежное вознаграждение.
Сразу несколько рационализаторских идей принадлежит инженеру-технологу Даниле Свечникову. Ему 24 года, в компании «ПРОМЭКО» трудится по специальности. Сейчас он получает высшее образование по направлению «электроэнергетика и электротехника», которое выбрал, потому что оно пригодится на производстве. В свою очередь, предприятие оплачивает учебный отпуск.
Фото: Андрей Заржецкий
— Бережливое производство — это хороший инструмент, который обязательно надо вводить на любом предприятии, — поделился мнением Данила Свечников. — Наиболее ценной из своих разработок считаю систему быстрой переналадки инструментов. Я сделал чертеж приспособления, которое действительно позволяет экономить время. Также я придумал специальную тележку, на которой транспортируется шнек. Устройство устанавливается в экструдер, где пластикат, который поступает к нам в гранулах, перерабатывается в вязкотекучую массу. Мы накладываем ее на токопроводящую жилу. Теперь переналадка, или замена шнека, происходит намного быстрее.
Кроме того, молодой сотрудник стал аккредитованным специалистом по бережливому производству и может проводить в компании семинары по шести темам. Это основы бережливого производства, системы 5С, организации рабочего места, отслеживания производственного анализа, а также картирование на производстве, то есть схематическое изображение процессов.